WA Compact – cost-effective and space-efficient solution
The WA Compact Welding System is an advanced and versatile solution engineered for making both continuous and stitch butt and fillet welds, using the MIG/MAG method. Equipped with a joint tracking system for active vertical and horizontal torch compensation, the WA Compact delivers enhanced precision without taking the space or cost of the gantry system.
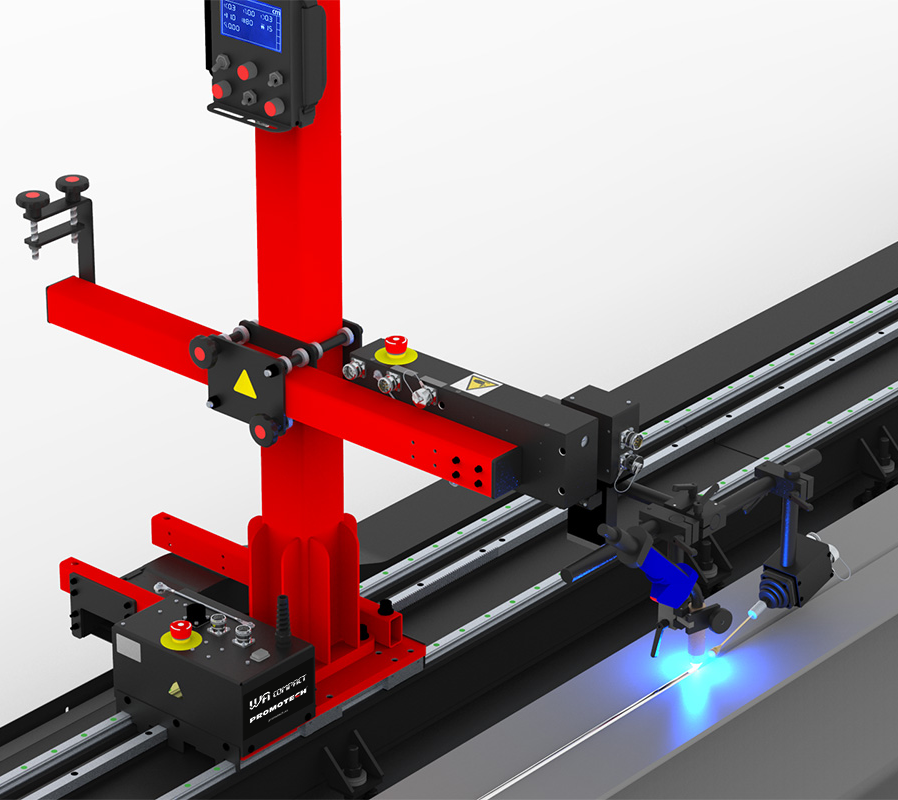
Users will surely appreciate the cost-effective and space-efficient nature of WA Compact. Positioned between a welding tractor and a compact gantry system, it combines the mobility of a trolley with the structural stability of a column-guided setup.
This makes the WA Compact a practical choice for both workshops and large-scale industrial operations— especially where space optimization is a priority.
WA Compact enables a wide range of welding joint applications.
This welding system can operate with or without oscillation, offering flexibility for a wide range of welding applications. It supports multiple oscillation patterns— straight, triangle, trapezoid, and square—which enhances its adaptability to different joint types and welding technology.
Path | Description |
---|---|
Triangle |
The machine travels only during oscillation. During oscillation dwell time, the machine stops to fill the crater. |
Trapezoid | The machine travels at all times, also during oscillation dwell time. |
Square |
The machine travels only during oscillation dwell time in left and right position. During oscillation, the machine stops. During oscillation dwell time in center position the machine fills the crater. |
The oscillator and motorized vertical slide keep the torch correctly aligned with the seam throughout the welding process. This ensures consistent penetration, proper fusion, and a smooth weld bead, while effectively preventing common defects such as undercut, porosity, and lack of fusion.
Ergonomic remote control pendant with simple and easy-to-operate control knobs makes adjustments possible even without lifting the operator’s welding hood. It allows the operator to conveniently set a wide range of parameters, including:
- Travel speed
- Torch height
- Oscillation offset
- Oscillation width: 0 to 114 mm (0–4 31/64″)
- Oscillation speed: 0.1 to 2 m/min (4–79 inch/min)
- Oscillation dwell time at the centre, left, or right position (0–5 seconds)
- Sensor rod tilt: in the Y-axis (current/initial) and Z-axis (current/initial)
When the stitch welding option is activated, the pendant also enables setting the following stitch-specific parameters:
- Weld length
- Space before welding
- Space between welds
- Total welding length – once this length is reached, the machine behaves as if a limit switch has been triggered
- Backweld length
- Crater fill time: before welding, at the weld end, and after welding
In addition, the operator can quickly switch between metric and imperial units (centimetres or inches) for added convenience.
Perfect Torch Alignment
WA Compact offers advanced joint tracking system designed to maintain optimal torch positioning. Operators can select between tracking in the Y axis, the Z axis, or both Y and Z axes simultaneously, depending on the application and their specific needs.
Y Axis Tracking (Lateral Tracking)
Tracking in the Y axis—the side-to-side direction—keeps the torch precisely centred over the weld seam without making unnecessary vertical adjustments. This mode is used when:
- the weld seam may shift horizontally due to material placement or distortion,
- the workpiece surface is flat and consistent in height,
- accurate centering of the torch over the seam is the primary goal.
Benefit: Optimal alignment along the seam with stable, controlled motion.
Z Axis Tracking (Vertical Tracking)
Tracking in the Z axis — the up-and-down direction — ensures consistent arc length and weld penetration, even when the surface height varies. This option is ideal when:
- the material surface is uneven, curved, or wavy (e.g., pipes, rolled plates),
- there are variations in material thickness,
- the weld seam is straight, but maintaining a consistent arc height is essential.
Benefit: Maintains steady arc parameters and high-quality welds in fluctuating vertical conditions.
Dual-Axis Tracking (Y + Z)
The Y + Z tracking mode is the most advanced option, enabling the system to dynamically adjust both the lateral and vertical position of the torch in real-time. Recommended for:
- complex weld geometries (curved or irregular seams),
- high-precision applications,
- automated production environments where repeatability and consistency are critical.
Benefit: Delivers maximum control, ensuring top-tier welding quality regardless of seam variability.
While full Y + Z tracking offers the highest level of control, in some applications tracking in just one axis is sufficient to achieve the desired accuracy. In the right context, limiting adjustments to a single axis means faster operation and shorter cycle times. However, for applications where precision, adaptability, and quality are critical, dual-axis Y + Z tracking remains the best choice to ensure flawless, repeatable welds.
Modular Track System for WA Compact
The WA Compact welding system travels along a modular track, delivering precise and stable movement throughout the entire welding process. While the standard minimum track length is 4 meters, the system is built from 2-meter support modules, allowing for highly flexible configurations. To meet specific project needs, the track can be extended using additional 2-meter long inner segments, up to a total length of 20 meters.
WA Compact – Technical specification
- Power 200 W
- Torch type MIG/MAG
- MIG/MAG torch diameter 16–22 mm (5/8″–55/64″)
- Horizontal speed 0,05–2,5 m/min (2–98 inch/min)
- Standard torch travel length * 3.5 m
- Standard overall track length * 4 m
- Oscillation type Linear
- Weld path Straight, triangle, trapezoid, square
- Oscillation width 0–114 mm (0–4 31/64″)
- Oscillation speed 0,1–2 m/min (4–79 inch/min)
- Oscillation dwell time at centre and on ends 0–5 s
- Maximum oscillator pulling force 50 N
- Weight 484 kg
The WA Compact is a cost-effective yet technologically advanced welding solution designed to boost productivity and minimize process time. Whether in shipbuilding, construction, or general fabrication, WA Compact delivers high-quality welds without compromising on performance—making it the perfect choice for industries where budget and space are limited, but weld quality is non-negotiable.